Air blast hydraulic Oil Cooler is used for maintaining oil temperature & viscosity. It removes heat gained due to frictional losses of hydraulic system of mobile or stationary equipment.In a Water Cooled Hydraulic Oil Cooler the oil is led along a bundle of copper pipes. At the same time coolant runs through these pipes and cools down the oil. A water cooled hydraulic oil cooler can be a very effective cooling system for intensively used hydraulic systems. When using a water-cooled oil cooler it is important to regularly inspect the cooler for contamination. When the water in a water-cooled oil cooler becomes contaminated this reduces the cooling capacity.
Water-cooled systems use cold water to remove heat, with hot and cold fluids separated by a barrier. Compared to air-cooled systems of equivalent capacity, water-cooled systems have lower up-front costs. They’re also quiet, compact, and do not alter the surrounding ambient temperature. Variations in air temperature have little or no effect on cooling capacity, which allows for greater consistency. Meanwhile, the system’s heated water can be used for other on-site purposes.
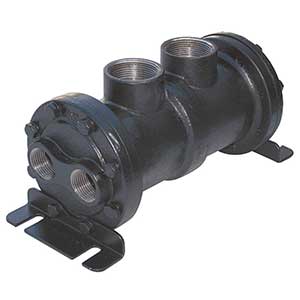
- Lubrication Oil System,
- Hydraulic Press,
- Hydraulic Oil Cooler and Oil Cooler for Mobile Trucks
- Food Process Industry,
- Power Generation,
- Hydraulic and Industrial Process,
- Mining & Construction Industry,
- Pharmaceutical industry
- Construction machinery (cranes, pumps, rotary drilling rig),
- Ship metallurgical and mining machinery and other hydraulic circuit cooling.
- corrosion resistance
- Long working life
- Minimum maintenance