Heat Recovery System Heat Exchangers:
Heat recovery system heat exchangers are the collection and re-use of heat arising from any process that would otherwise be lost. The process might be inherent to a building, such as space heating, ventilation and so on, or could be something carried out as part of business activity, such as the use of ovens, furnaces and the like. Heat recovery system heat exchangers can help to reduce the overall energy consumption of the process itself, or provide useful heat for other purposes. Heat recovery system heat exchangers unit is an energy recovery heat exchanger that recovers heat from hot streams with potential high energy content, such as hot flue gases from a diesel generator or steam from cooling towers or even waste water from different cooling processes such as in steel cooling.
Image:
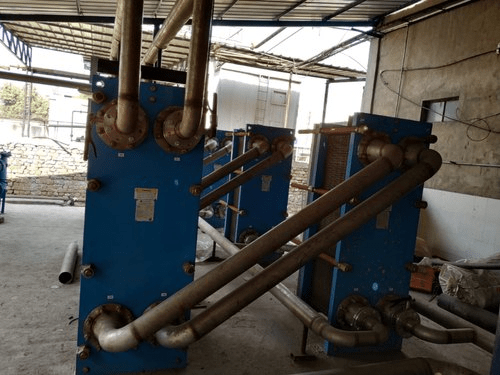
Process:
Heat recovery system heat exchangers are heat found in the exhaust gas of various processes or even from the exhaust stream of a conditioning unit can be used to preheat the incoming gas. This is one of the basic methods for recovery of waste heat. Many steel making plants use this process as an economic method to increase the production of the plant with lower fuel demand. There are many different commercial recovery units for the transferring of energy from hot medium space to lower one. The addition of heat recovery means that some of the heat contained within the extract air can be recovered. The heat energy is passed into the incoming fresh air effectively pre-heating it and meaning the boiler needs to add less heat. The two air streams need not mix directly to allow the transfer of heat.
Advantages:
- The recovery process will add to the efficiency of the process and thus decrease the costs of fuel and energy consumption needed for that process.
- Reduction in Pollution: Thermal and air pollution will dramatically decrease since less flue gases of high temperature are emitted from the plant since most of the energy is recycled.
- Reduction in the equipment sizes: As Fuel consumption reduces so the control and security equipment for handling the fuel decreases. Also, filtering equipment for the gas is no longer needed in large sizes.
- Reduction in auxiliary energy consumption: Reduction in equipment sizes means another reduction in the energy fed to those systems like pumps, filters, fans,…
Benefits:
- Very low noise levels – essential as MVHR systems are constant-running
- Options to suit all property sizes and types, saving you space and money
- Compact, lightweight and easy to install
- Fan controls designed for quick and easy commissioning
- Full design and solution package available
- 5 year warranty for peace of mind
- Options for summer bypass and integral frost protection
- Significant energy savings with very low running costs
- Low maintenance and easy access filters (no tools required)
- Reduced carbon emissions
- Less heat is wasted from the primary process
- Energy costs are significantly saved
- Heat costs are lowered
Applications:
Airports, Hospitals, Hotels, Warehouses and Offices as well as manufacturing applications including Food and Drink, Plastics and Rubber, Metals and Pharmaceutical and Laboratory requirements, allowing for industrial heat recovery to be achieved.