Gasket Plate Heat Exchangers were first produced in the 1920s and have since been widely used in a great number of sectors. A plate exchanger consists of a series of parallel plates that are placed one above the other so as to allow the formation of a series of channels for fluids to flow between them.
The space between two adjacent plates forms the channel in which the fluid flows. Inlet and outlet holes at the corners of the plates allow hot and cold fluids through alternating channels in the exchanger so that a plate is always in contact on one side with the hot fluid and the other with the cold. Generally, these plates are corrugated in order to increase the turbulence, the thermal exchange surface and to provide mechanical rigidity to the exchanger. Corrugation is achieved by cold forging of sheet metal with thicknesses of 0.3mm to 1 mm.
The most frequently used materials for the plates are stainless steel (AISI 304, 316), titanium and aluminium. The corrugation on the plates forces the fluid on a tortuous path, setting a space between two adjacent plates b, from 1 to 5 millimetres. The fluids can cross the channels in series (a less common solution) or in parallel by making counter-current or current configurations.The serial configuration is used when there is a small flow rate for each fluid but high heat jump; the greatest problem is with a high pressure drop and an imperfect counter-current.
The parallel configuration with counter current channels is used for high flow rates with moderate temperature drops, and is the most widely used.When there is a great difference between the flow rates (or between the maximum permissible pressure drop) of the two fluids, the exchanger can run twice by the fluid with a lower flow (or higher losses) to balance the values of pressure drops or specific flow rates in the channels.
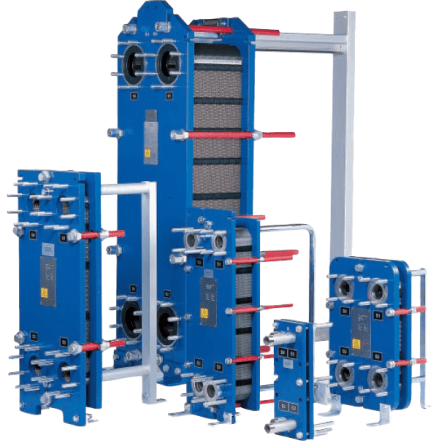
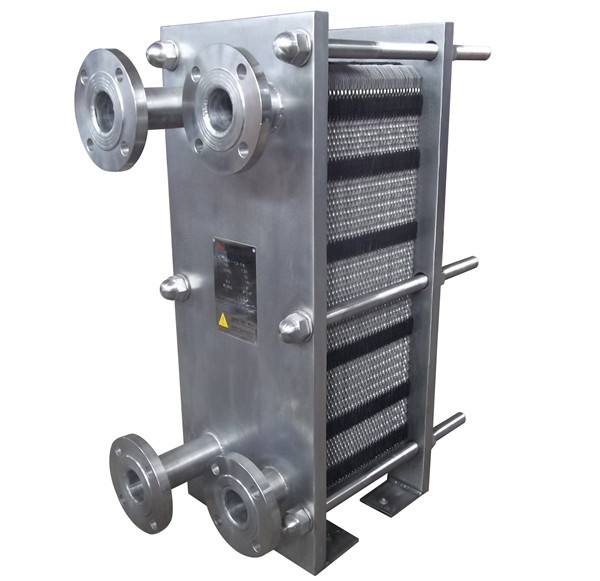
Gasket Plate Type Heat Exchangers Advantages
- Compact design
The combination of high value for the overall heat transfer coefficient and the general compact configuration of the flat plate heat exchanger lead to its ability to have the same thermal capacity as a shell and tube heat exchanger as much as five times its size
- Easy maintenance and cleaning
The fact that a plate and frame heat exchanger can be taken apart as discussed in the previous section, allows for easy cleaning and maintenance. A plate and frame heat exchanger can be designed to allow for easy addition or removal of plates to expand or reduce its heat transfer capacity.
-
A flat plate heat exchanger works well with small temperature differences between the hot fluid and the cold fluid.
-
High value for overall heat transfer coefficient, for the same two fluids, a flat plate heat exchanger typically has a U value much higher than either a shell and tube heat exchanger or a spiral heat exchanger.
-
Capacity can be increased by introducing plates in pairs of heat exchanger.Plate type heat exchanger is Maintenance simple and can be easily cleaned.
-
Turbulent flow help to reduce deposits which heat transfer, No extra space is required for dismantling in Plate heat exchangers.