Fixed tube heat exchangers is the most common type of heat exchanger in all Industries. Mostly used in higher-pressure and Higher Temperature applications. In this type of exchangers the tube sheet is welded to the shell and no relative movement between the shell and tube bundle is possible.
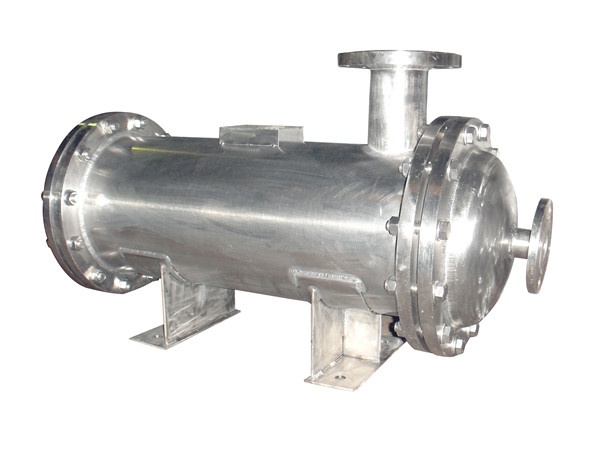
The tube sheets at both ends of the fixed tube-sheet heat exchanger are connected and fixed with the shell by means of the welding method. Sixed tube-sheet type heat exchanger features simple and compact structure, and low manufacturing cost for the same diameter of shell, the biggest number of caldaria is available in tubular heat exchangers is widely applied in engineering. The Fixed tube-sheet heat exchanger are that shell pass cannot be cleaned with the mechanical method and the maintenance is difficult. The Fixed tube-sheet heat exchanger is applicable to all services where the temperature difference between the shell and tube is small, the temperature difference is slightly great but the pressure of shell pass is not high with media in the shell pass not easy to scale, or the shell pass can be cleaned with chemical method after the scaling is formed.
In Fixed tube heat exchangers Air heater is an important Boiler auxiliary which primarily preheats the combustion air for rapid and efficient combustion in the furnace. The air heater recovers the waste heat from the outgoing flue gas of a Boiler and transfers the same to the combustion air. In a utility Boiler the flue gas leaves the economizer at a temperature of around 3800C. As every 550C drop in flue gas temperature improves the Boiler efficiency by about 2.5%, having an air heater in the downstream of economizer the Boiler efficiency is considerably improved. Further the air heater may also be iised for heating the air to dry the coal in the pulverizing plant.
- The Boiler efficiency is increased.
- More stable combustion in furnace.
- The combustion is intensified with the use of hot air.
- Lower grades of coals can be burnt efficiently with hot-air.
- The use of hot air, improves the heat transfer rate and so less heat transfer area will be required.
- The combustion is made complete with negligible amount of carbon in ash.
- Faster load variations are possible.
- The coal can be dried effectively for easy pulverization and combustion.
- The Boiler efficiency is increased.
- More stable combustion in furnace.
- The combustion is intensified with the use of hot air.
- Lower grades of coals can be burnt efficiently with hot-air.
- The use of hot air, improves the heat transfer rate and so less heat transfer area will be required.
- The combustion is made complete with negligible amount of carbon in ash.
- Faster load variations are possible.
- The coal can be dried effectively for easy pulverization and combustion.
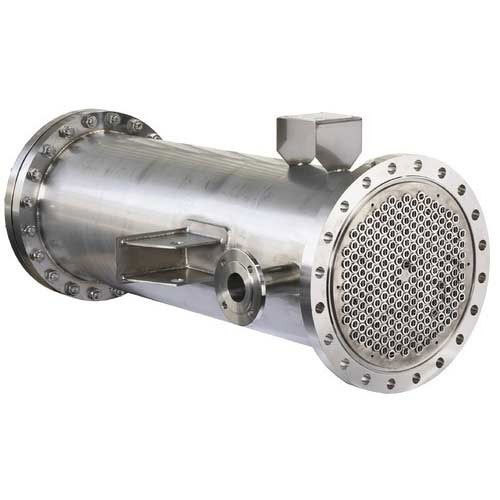